Cavitation Abrasive Surface Finishing
Cavitation Abrasive Surface Finishing is a processing technology that removes abnormal layers from the surface of objects like additive manufacturing metal parts or die cast parts. CASF also smooths surfaces, and imparts compressive stress through a cavitation effect generated by injecting high-pressure water into a tank filled with an abrasive suspension.
For example, during the layered molding process of parts made with a metal 3D printer, abnormal layers can form due to poor melting. Cavities frequently occur from the surface layer to a depth of approximately 150 μm.
With CASF processing technology, abnormal layers can be removed, surfaces are smoothed, and compressive stress is applied to increase fatigue strength and improve fatigue life.
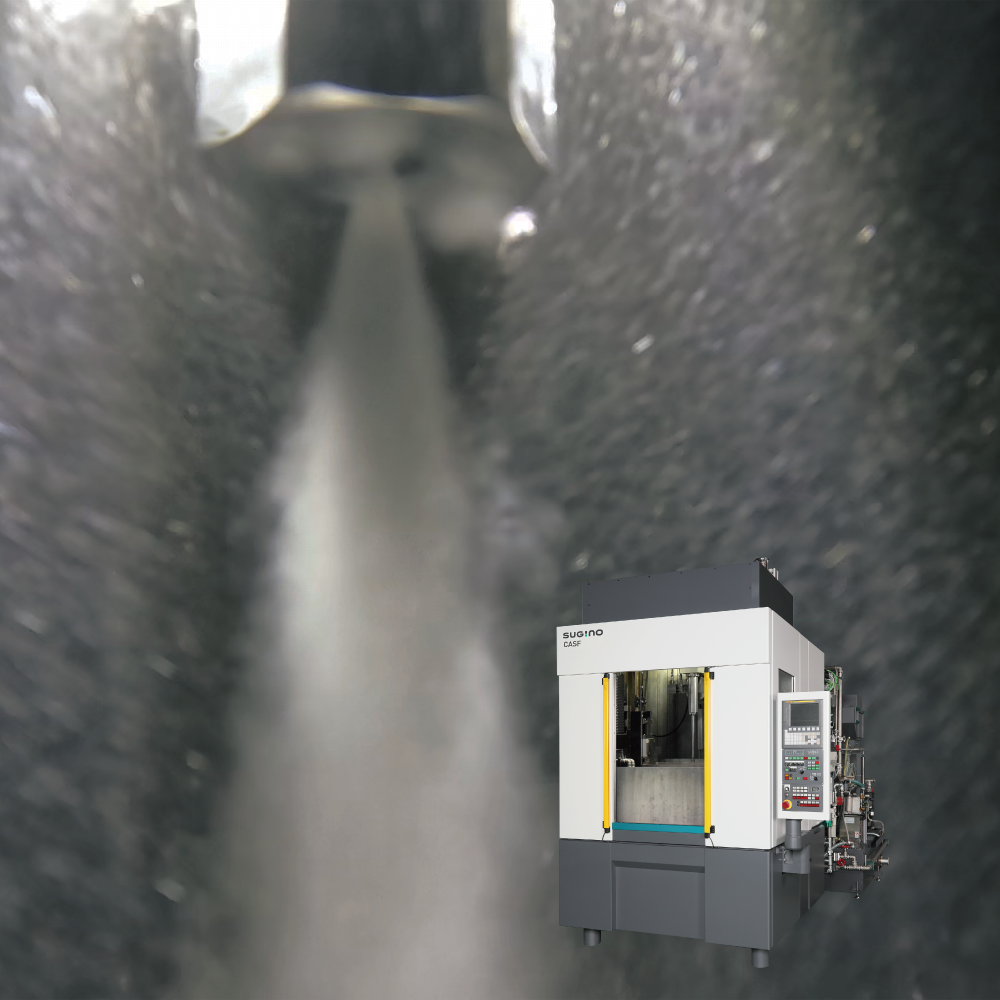
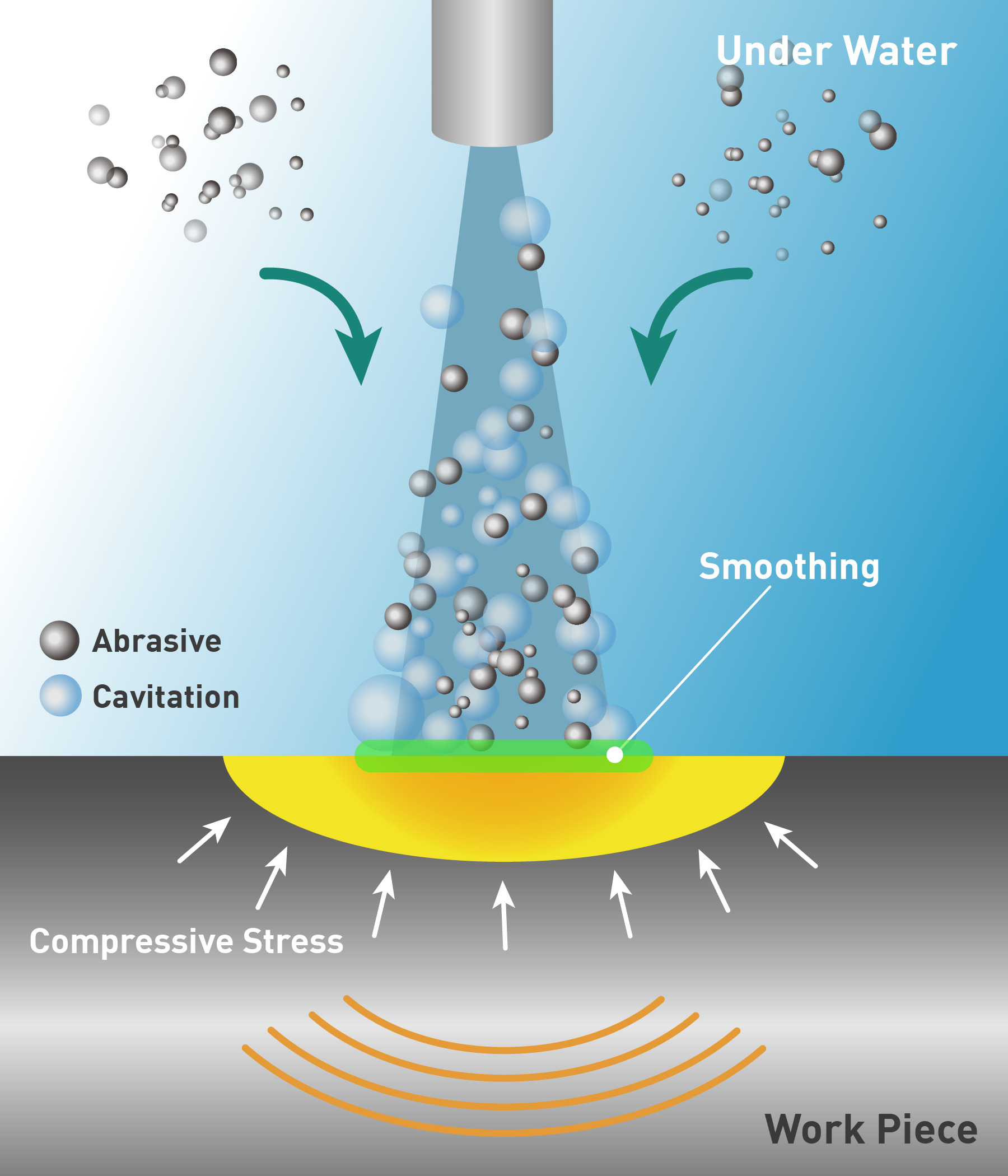
How CASF Works
Advantages
Removes abnormal layers or support structures from metal additive manufacturing parts (AM parts).
Improves surface roughness.
Increases fatigue strength and improves fatigue life cycle.
Able to reach inner diameter for surface finishing.
Applications
AM Parts, Die Cast Parts, Metal Casting
Removal of abnormal layers from metal additive manufacturing parts (AM parts)
Metal additive manufacturing parts (AM parts) have abnormal layers, such as poor fusion and microcracks, that happen at positions approximately 150 μm from the surface during the manufacturing process.
If abnormal layers are present, there is a risk of component breakage and insufficient fatigue strength. Additionally, any remaining unmelted metal powder on the surface increases the frictional resistance of fluids.
With CASF, smoothing can be performed up to 200 μm below the surface.
Removing abnormal layers and unmelted metal powder imparts compressive stress, improving the component's fatigue strength.
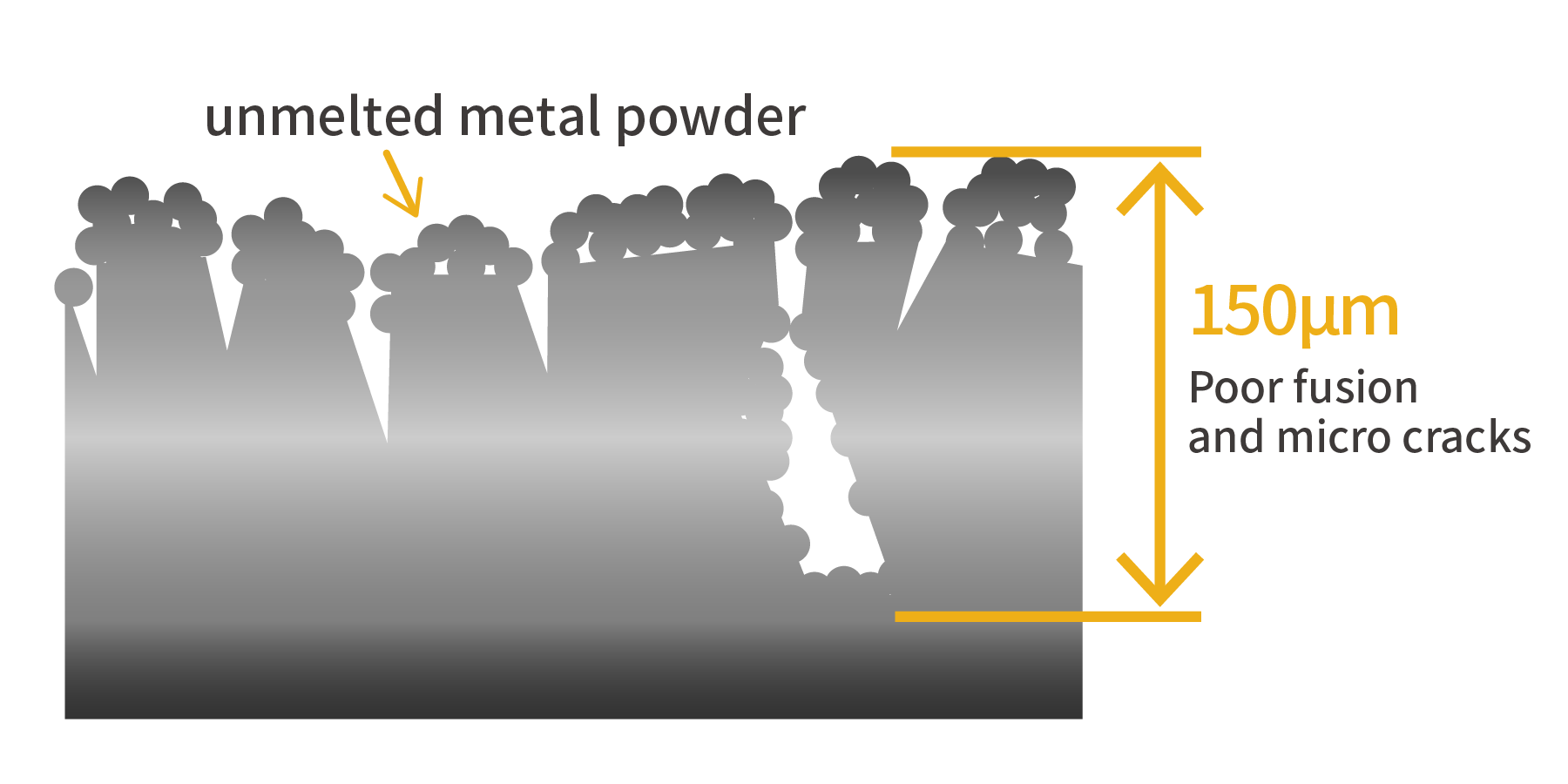
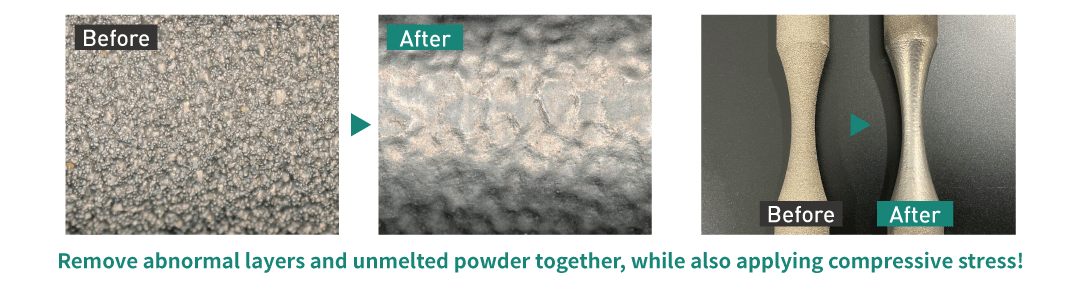
Remove support structures from metal additive manufacturing components (AM parts).
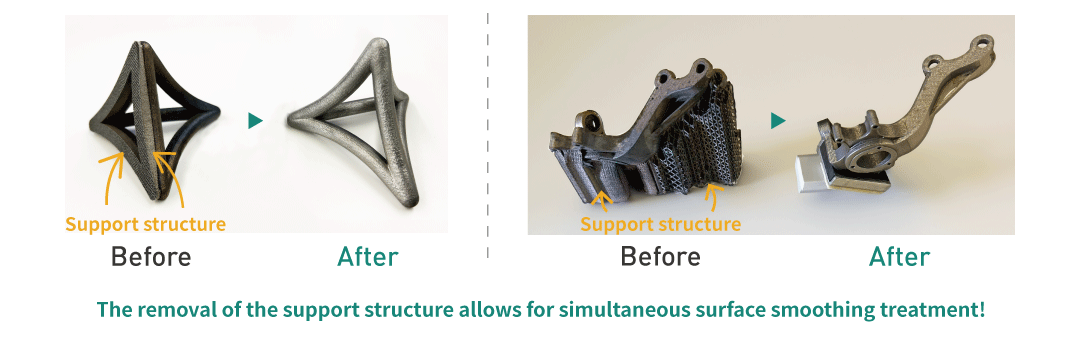
Improve surface roughness and fatigue strength
The CASF process improves surface roughness, fatigue strength, and fatigue life through compressive stress.
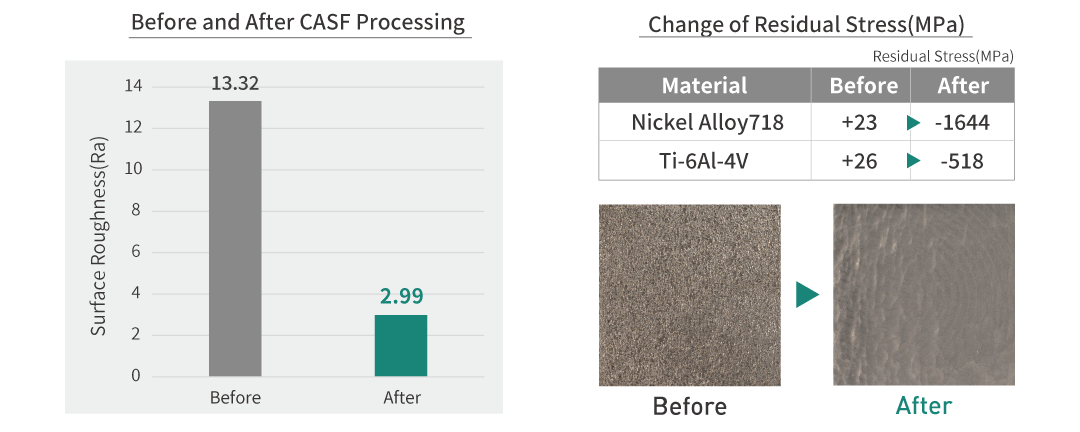
Capable of Reaching Inside Diameter Surface
CASF can reach and treat the inside diameters of flow pipes and other hard-to-reach areas. Other methods that use standard media can only affect the area that the media can make contact with.
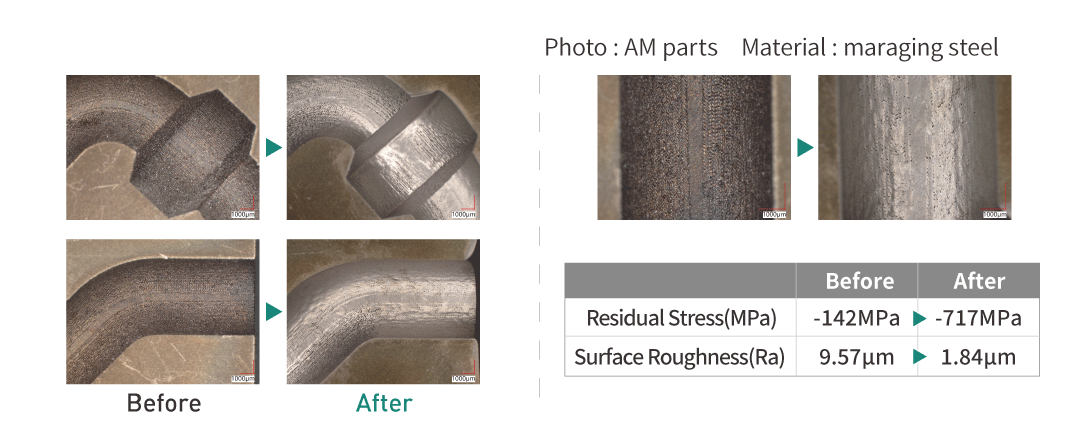
Uniformly improves the surface roughness of down-skin
In metal additive manufacturing (AM), the surface roughness varies significantly depending on the build angle.
Particularly, the down-skin at around 45° has the roughest surface, posing challenges due to difficult access and increased effort required in post-processing.
With CASF, fluids act on all corners/areas of AM parts, allowing for uniform surface treatment in a single operation.
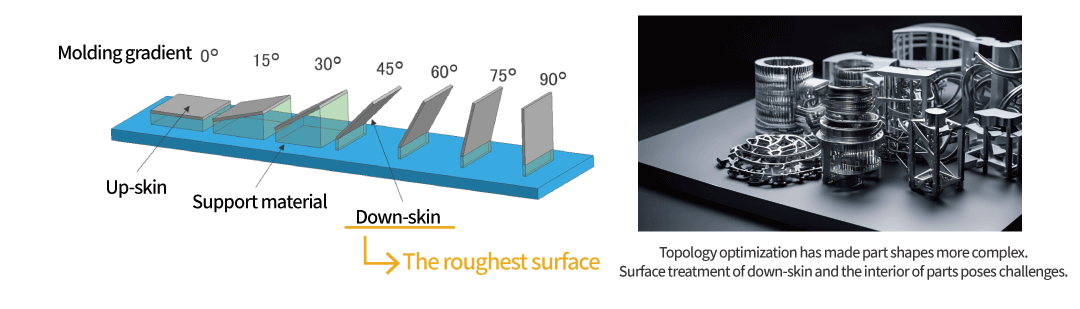
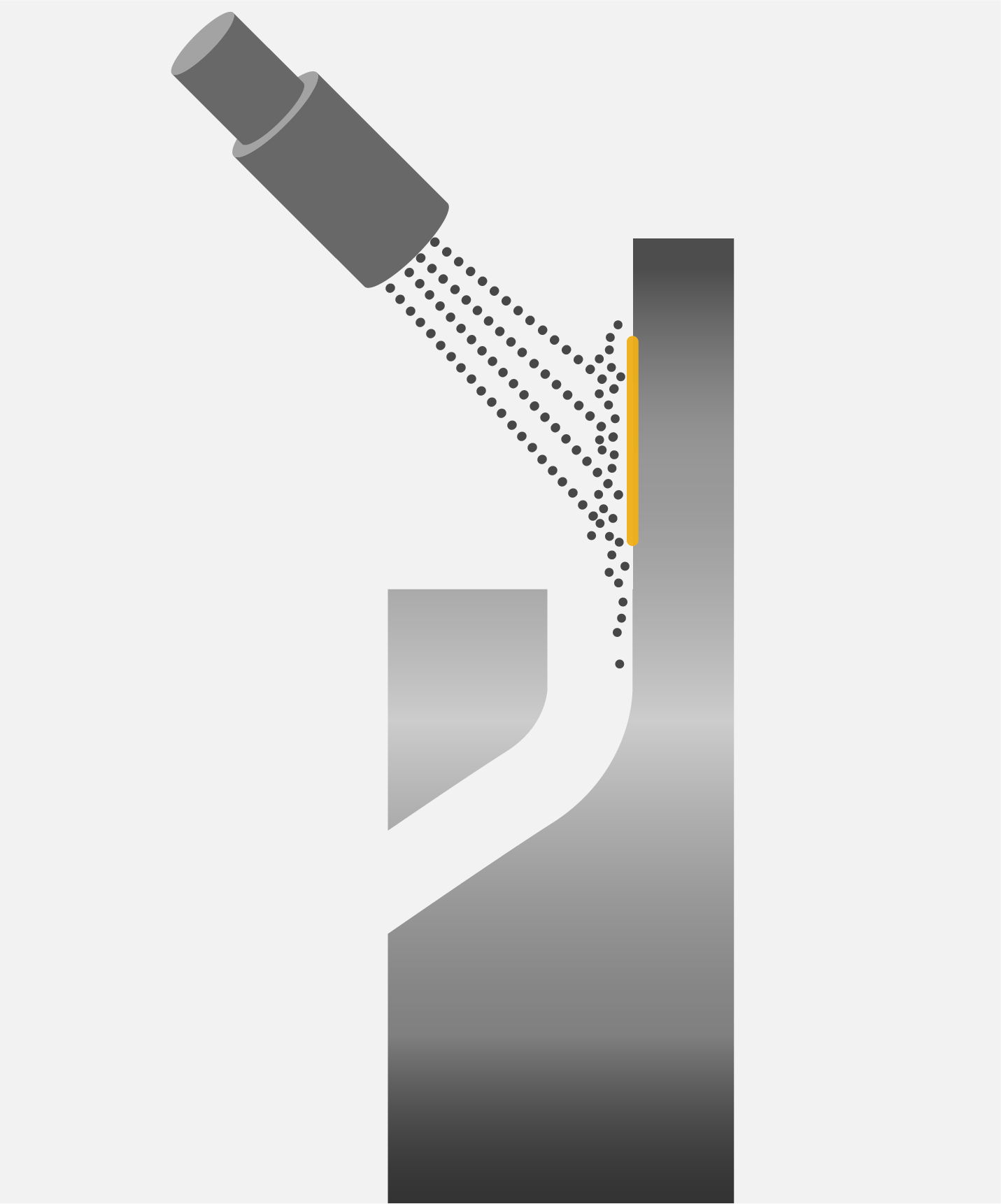
Surface Finishing Using Only Media
Affects only areas where
the media makes contact
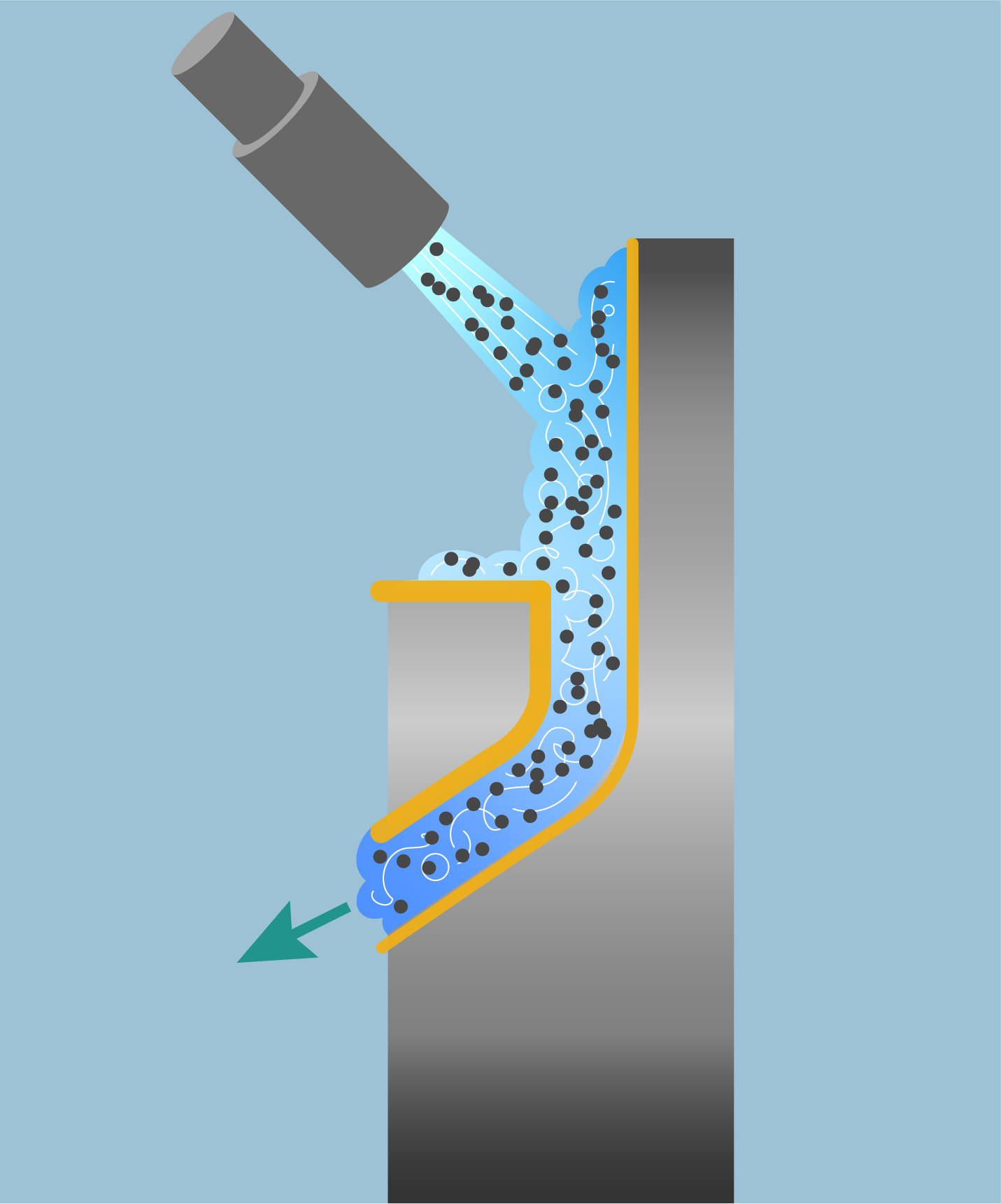
CASF
Uniform surface treatment for
every corner of the part
Controller
FANUC 0i-MF Plus
Machine Dimensions
W 1,600 × D 2,700 × H 2,500 mm
Machine Weight
4,300 kg