This week, we’re taking a look at CNC controls in deburring and parts cleaning. What is CNC? And how it can be used with these technologies?
Combining CNC controls with high-pressure water deburrs and cleans parts in one eco-friendly process, removing burrs and loose chips even in deep holes – all while leaving the part clean and free of debris.
So, what is CNC exactly?
Computer Numerical Control, CNC, is the automated control of machining tools (such as drills, lathes, mills) by means of a computer. A CNC machine processes a piece of material to meet specifications by following a coded program – a series of instructions that guide the machine’s speed, feed rate and coordinate the movements. The program can run without a manual operator directly controlling the machining operation. CNC excels at manufacturing parts or components that be difficult to create manually – and it does so with precision, accuracy, and repeatability. In modern machining, CNC programs can take a billet or block of metal and through a combination of drilling, milling, turning, or other types of machining operations, can create a complex part.
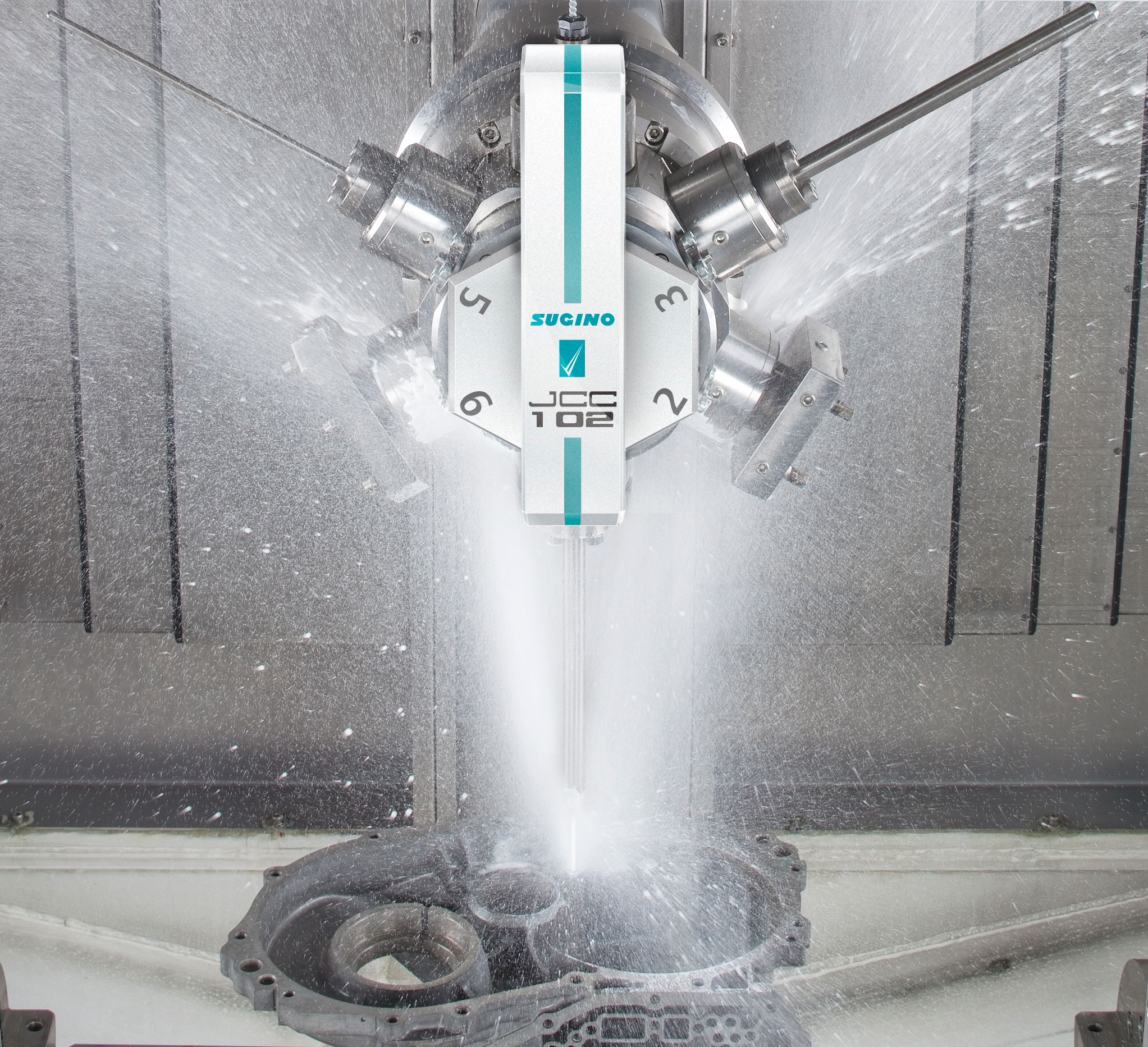
Sugino’s deburring and part cleaning machines deliver precise results through high-pressure water and CNC control.
In this manner, CNC can also be employed to direct and position high-pressure water to accurately and effectively wash and deburr parts within a cleaning center. Like tools, pressurized water can be programmed and run through a variety of carefully chosen nozzles to run those same paths that created the part. Sugino’s skilled engineers create these CNC programs in the same way – and the benefits of CNC, combined with decades of experience harnessing the power of water – deliver precise, repeatable deburring results and cleaner workpieces.
When we talk about a CNC machine – it refers to a motorized maneuverable tool and often a motorized maneuverable platform, which are both controlled by a computer that gives the machine specific input instructions. CNC machines are a blend of technology and real-world tooling.
G-Code and M-Code
Instructions are delivered to a CNC machine in the form of a sequential program of machine control instructions such as G-code and M-code. Then, those instructions are executed as a program.
Some key points about M-code and G-code:
- M-codes operate the machine, while G-codes are responsible for the movement of the cutting tools (lathe/mill/waterjet) or cleaning/deburring paths
- The program can be written by a person or, far more often, generated by graphical computer-aided design (CAD) software and/or computer-aided manufacturing (CAM) software
- G-code is the most widely used CNC programming language
Next week, we’ll look at the role of each axis in the machining process – and show you how that also plays a role in deburring and washing programs.