JCC 104 4+1
Reach, deburr, and clean all six sides of your workpiece.
It's our most powerful deburring and cleaning solution yet. The 104 combines indexing 4+1 control and high-pressure water jet deburring to handle hard-to-reach places where burrs hide. With a newly developed hollow 2-axis tilting rotary table with an open bottom, all 6 surfaces can be free of chips and burrs, clean, and ready to go. All packed into an energy-efficient, streamlined solution.
Take a look and click on the key features to learn how the Hybrid's powerful deburring and part cleaning can reduce time and labor in your process - while accessing all sides of your part.
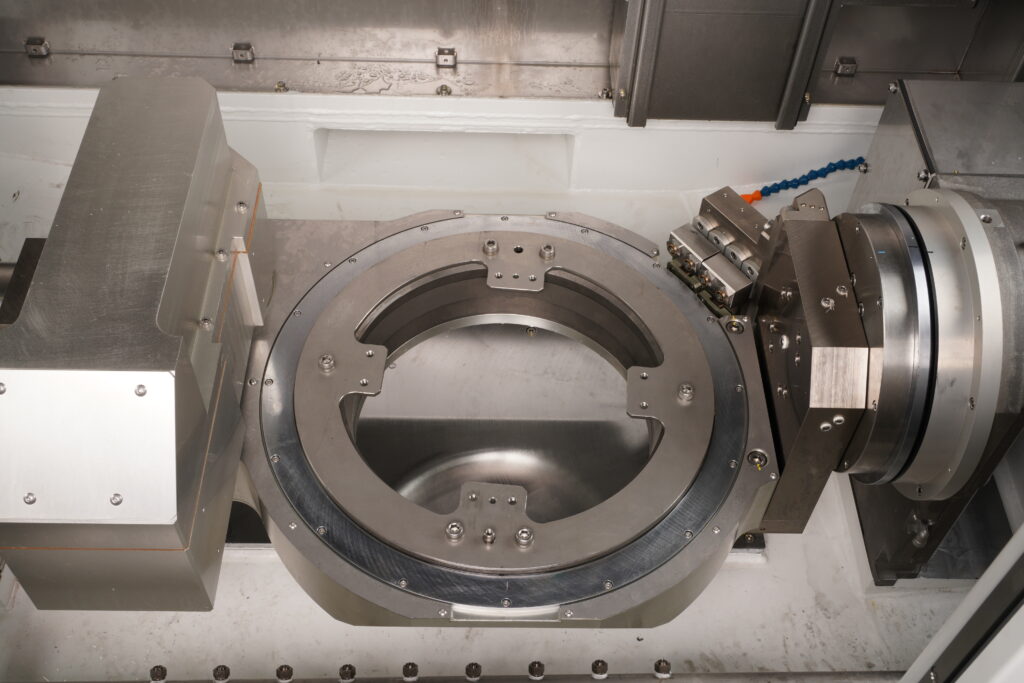
Access all surfaces of the workpiece.
Equipped with a newly developed hollow 2-axis tilting rotary table with an open bottom for deburring and cleaning all surfaces. The 5-axis indexing control allows deburring on all surfaces of the workpiece, including the mounting surface.
Deburr and clean with the power of high-pressure water.
High-pressure water of up to 50MPa can deburr areas where tools cannot reach, such as cross holes, deep holes, and stepped areas.
In addition, deburring with high-pressure water also cleans at the same time, allowing the processes to be consolidated.
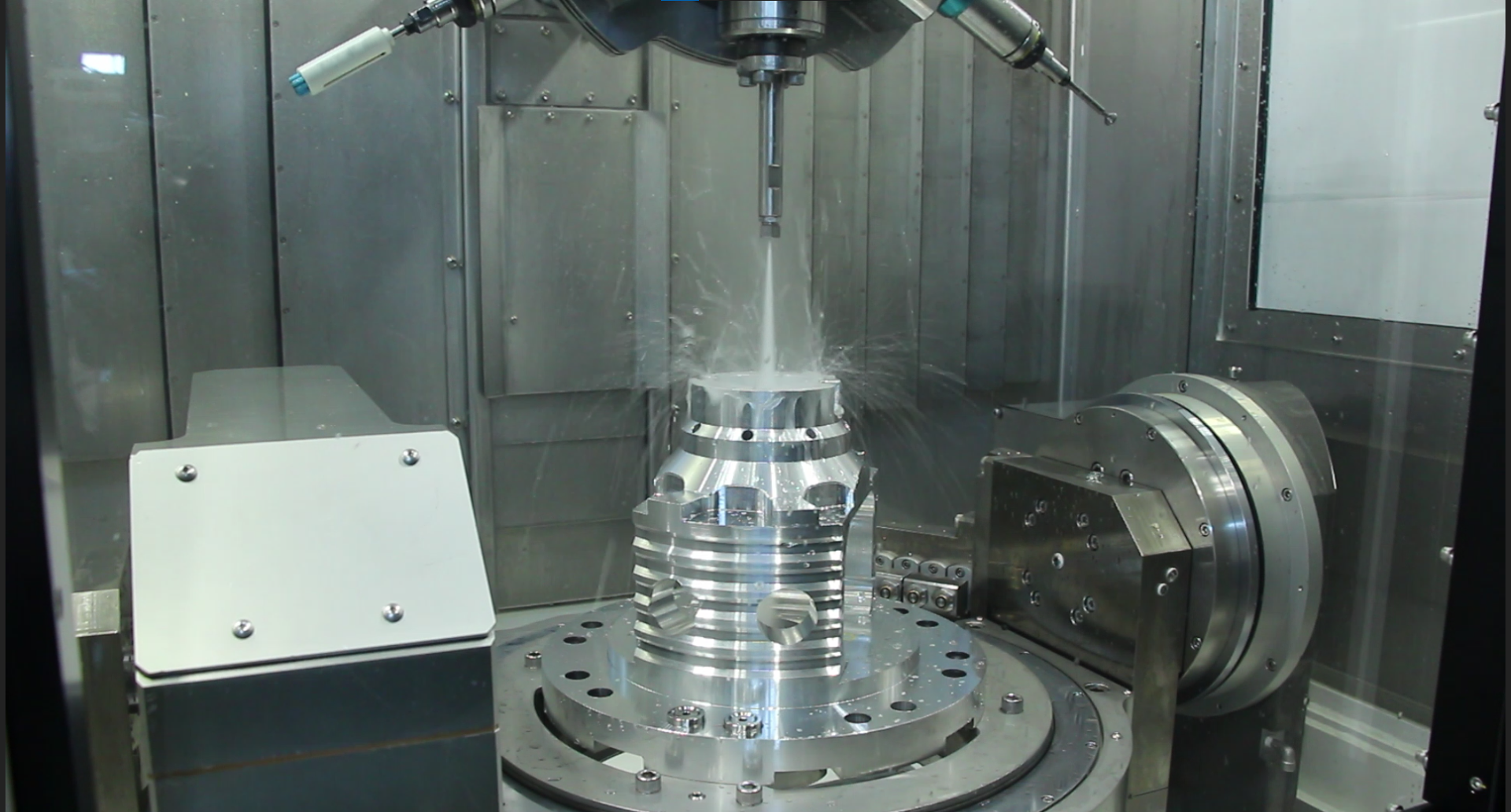
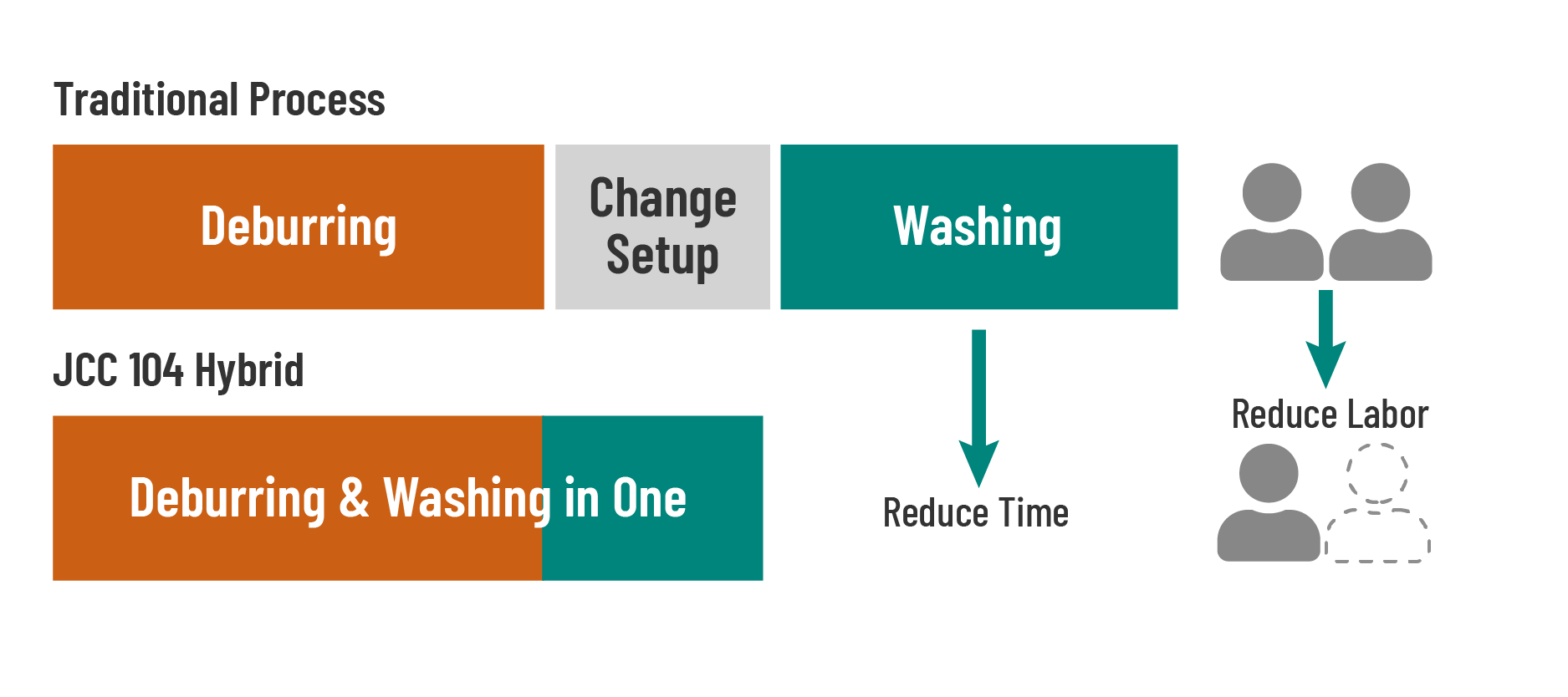
Consolidates cleaning and deburring processes for improved productivity.
The deburring process is often done manually and requires a lot of time and cost. The 104 Hybrid can perform highly accurate deburring and cleaning all at once, contributing to automation and labor savings, and improving productivity.
Equipped with the JCC-eSmart energy-saving package.
JCC-eSmart is standard on all JCC models. It optimizes the power of the high-pressure water generation pump (which uses the most power in a parts washer) and significantly reduces power consumption.
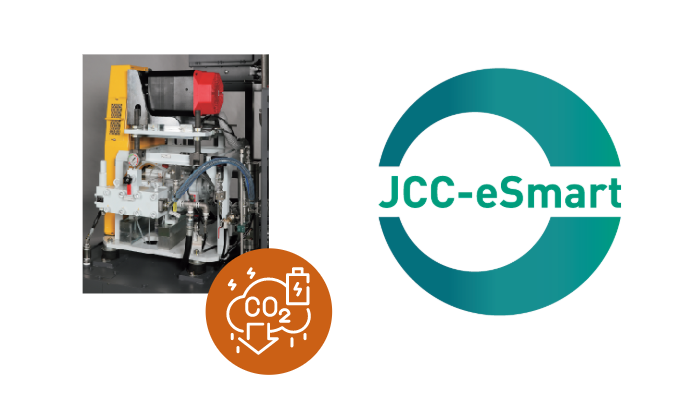
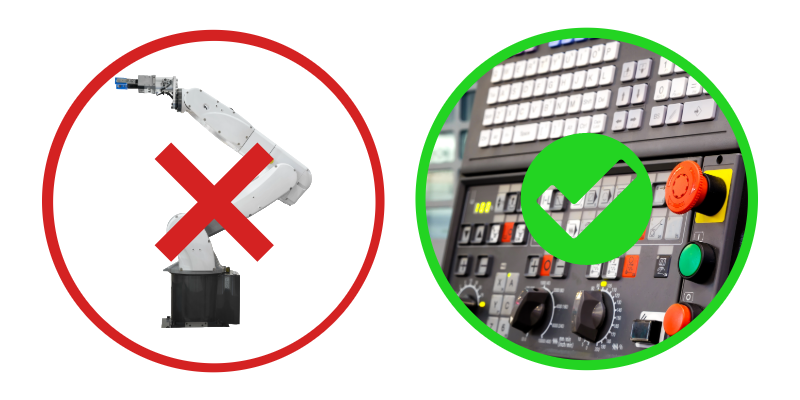
Easy to operate with CNC control.
Controlled by CNC, the JCC Hybrid can be operated using the familiar G code. Because it does not rely on the complicated instructions, special skills, or qualifications that robots require, anyone can use it.
Cleaning Pressure
Max. 50MPa
Flow Rate
Max. 29L/min
Stroke
X axis: 750mm, Y axis: 500mm, Z axis: 500mm
Rapid Traverse Speed (X, Y, X axis)
60m/min
Number of Tools
6
Control Device
FANUC 0i-MF Plus
External Dimensions (Equipment Body)
Width 1,600mm x Depth 2,700mm x Height 2,500mm
Machine Mass (Equipment Body)
4300 kg
Our robust parts testing process can show you exactly how JCC can benefit your production process.
We offer parts testing at our Wixom Technology Center. And our results report is second to none. To discuss your project or testing, get in touch - or request a call or email at your convenience.
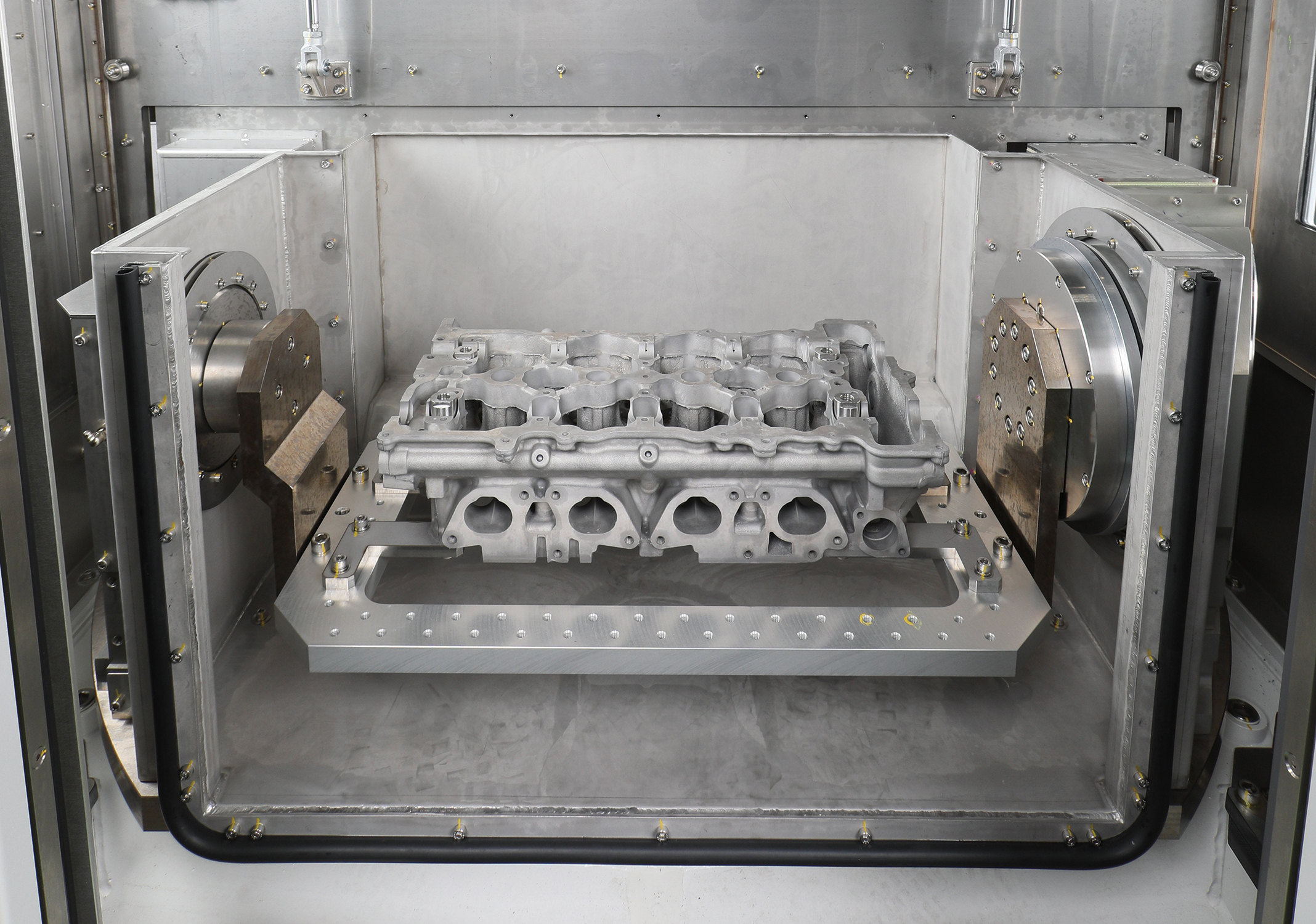
Explore More Deburring and Parts Cleaning Content
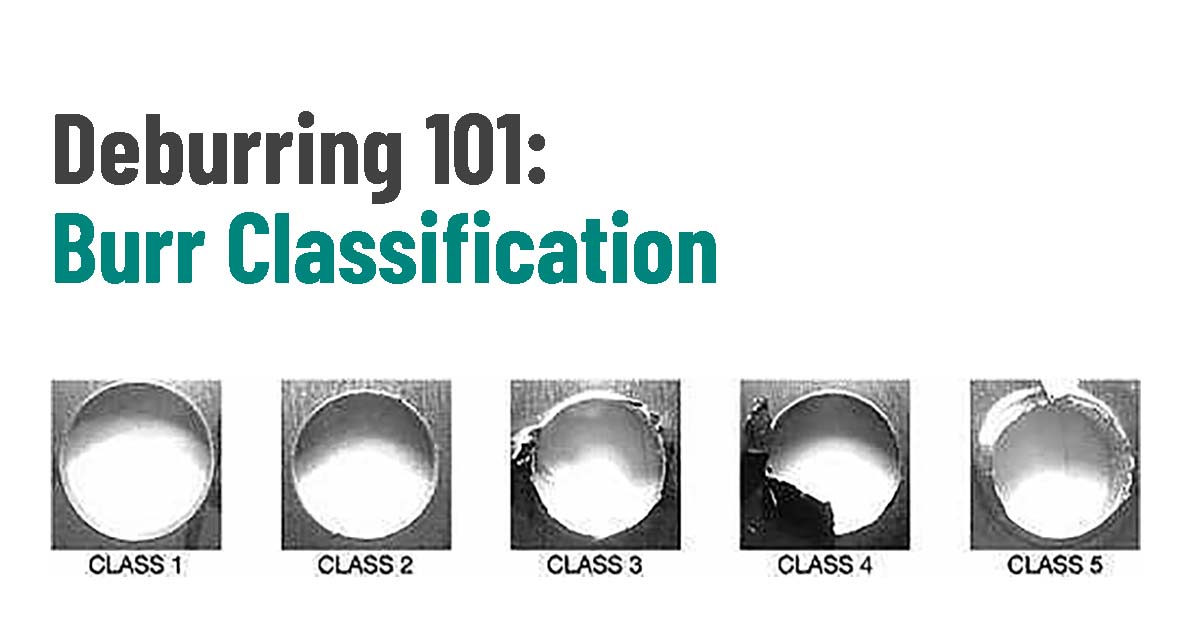
Classification of Burrs
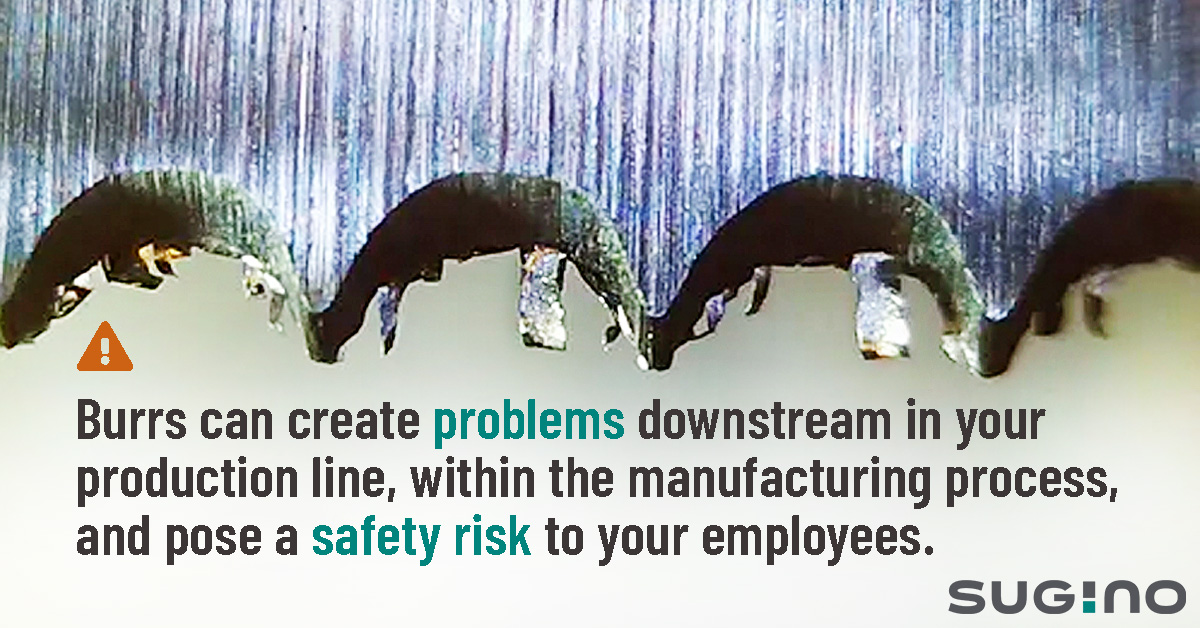
Problems Burrs Create
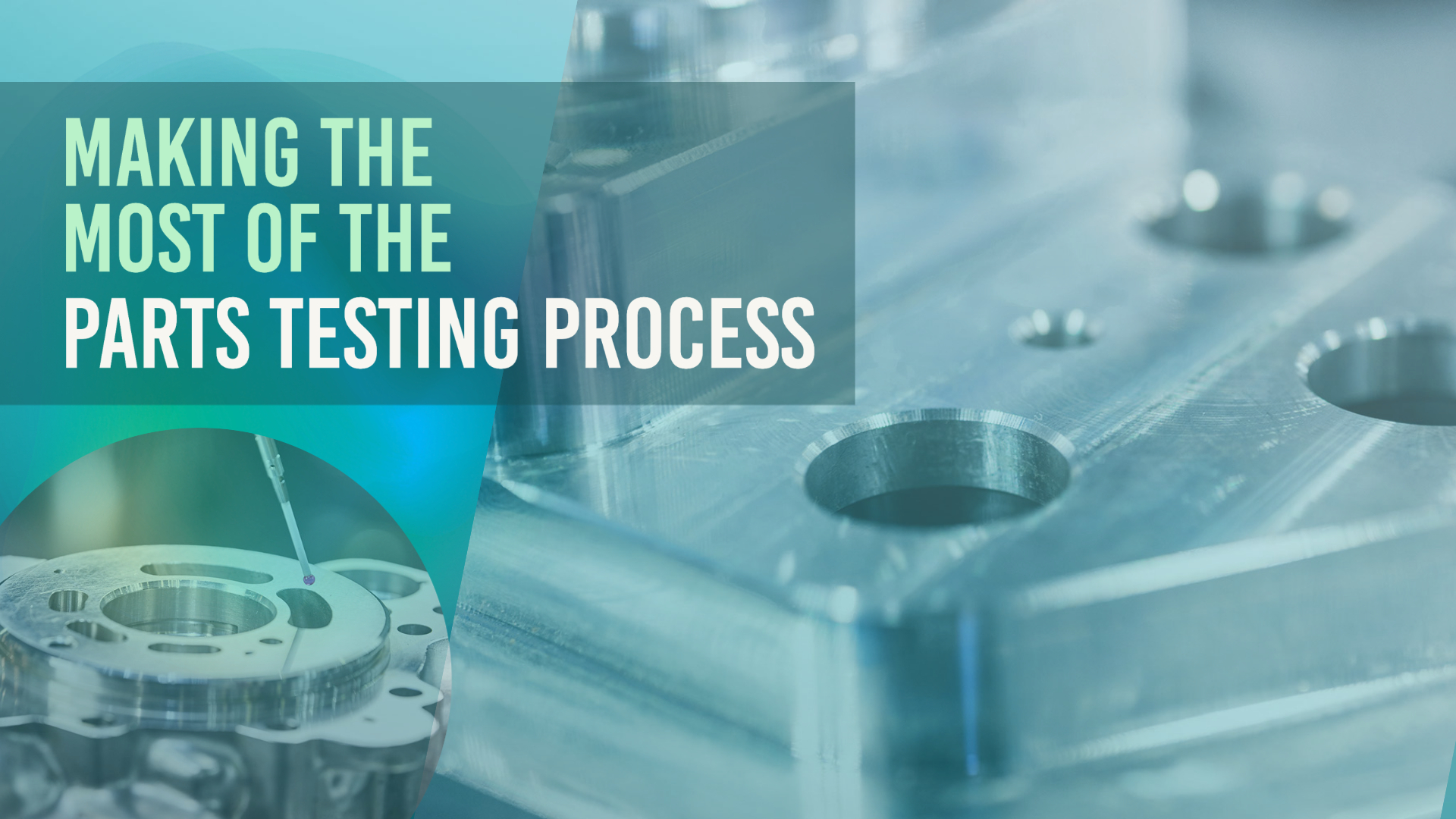
The Parts Testing Process
A guide to getting the most out of the parts testing process for deburring. From sending parts to working with your sales engineer.