Processing Raw Materials – Chamber Types
Star Burst, Sugino’s full line of wet jet milling devices, disperse, emulsify, pulverize, and reform surfaces of raw materials by collision, cavitation, and high shear generated by high pressure up to 245 MPa with the aqueous jet at the relative velocity of Mach 4. Star Burst does not use any grinding media and can deliver homogenized particle size with minimal contamination. Star Burst can be customized based on the client’s requirements and the materials being processed. Customization options include several chamber types that perform different functions for processing raw materials. Choosing the right chamber can optimize output based on application, such as dispersion, pulverization, emulsification, circulation cooling, etc.
Our sales engineers can customize and build the machine to meet your exact specifications. Regardless of material, application, and volume.
Oblique Collision Chamber
Atomization is performed by obliquely colliding raw materials with ultra-high pressure.
Applications: Dispersion, pulverization, emulsification, surface modification.
Ball Type Chamber
Raw material is injected at ultra-high pressure and atomized by colliding with ceramic balls.
The unique non-linear ball and nozzle design minimizes contamination due to wear.
It is effective for pre-dispersing raw materials with many large particles that tend to clog or at low pressure.
Applications: Dispersion, pulverization, emulsification.
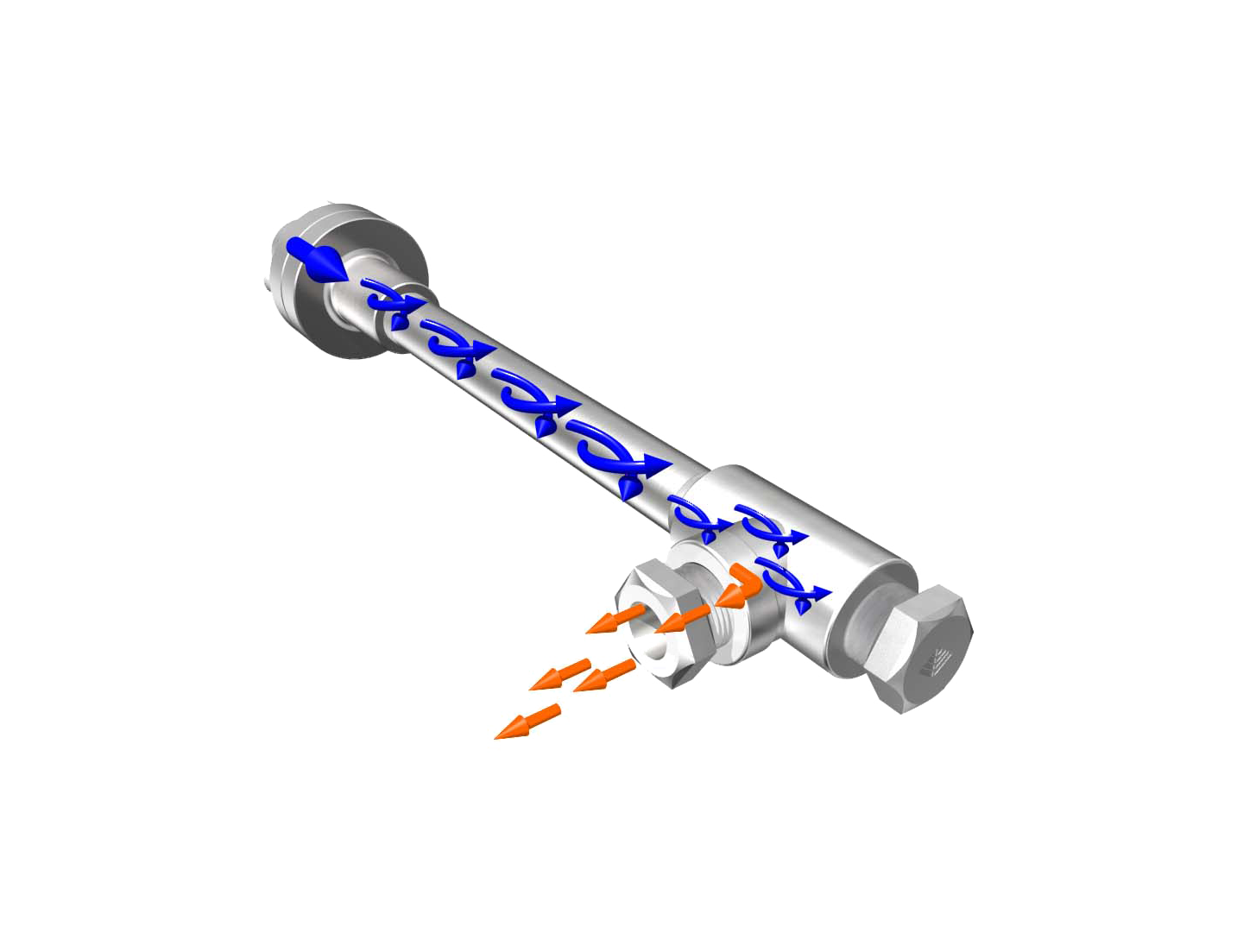
Single Nozzle Chamber
Dispersion and exfoliation are performed by cavitation and turbulence when injected into the liquid (into the raw material) at ultra-high pressure.
It is effective for cleaving layered minerals (mica, montmorillonite, etc.) and raw materials that crack when a force is applied locally.
Application: Dispersion, exfoliation
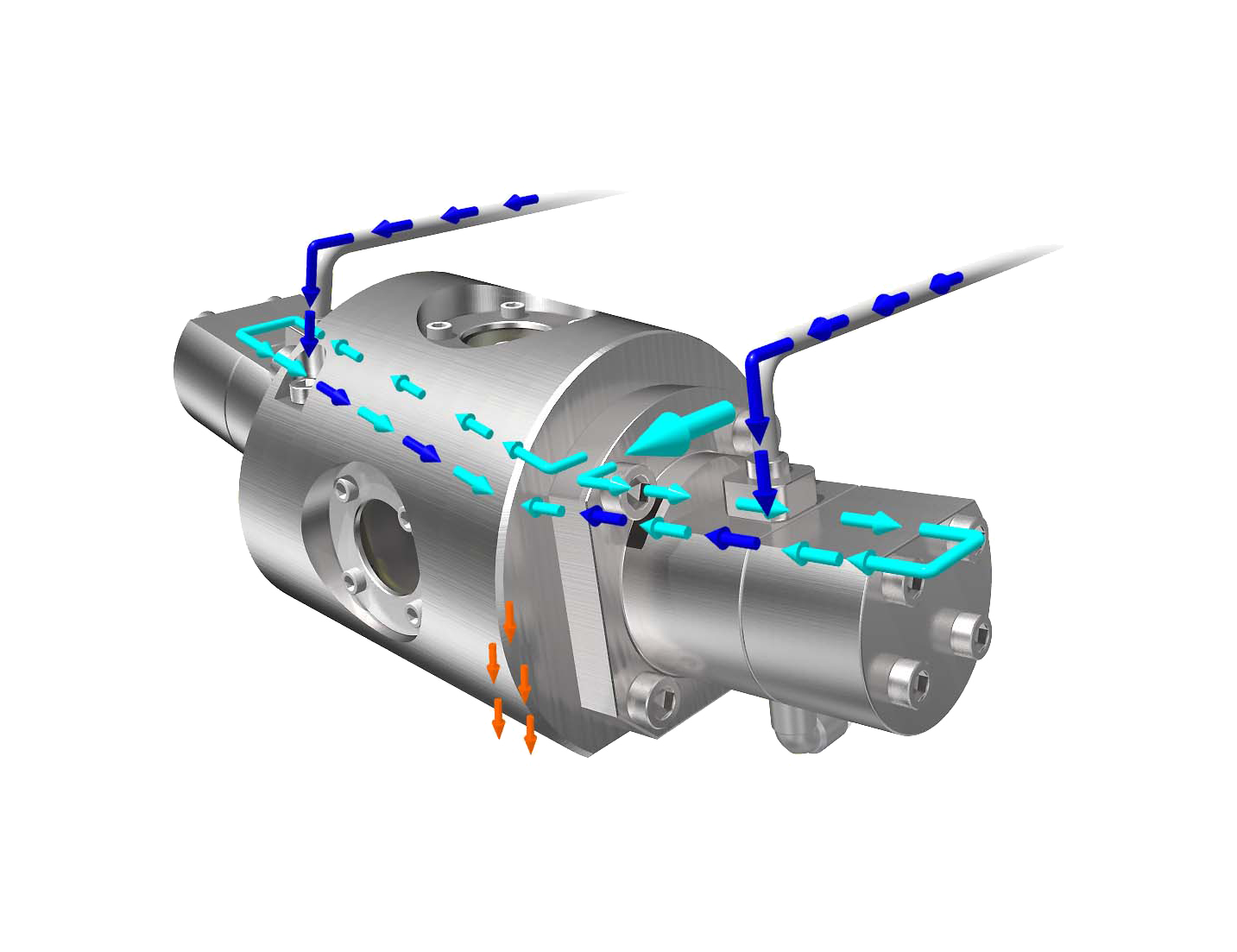
Separation Chamber
Designed for high specific gravity or ductile materials such as aluminum, nickel, or other similar metals, this chamber minimizes the deformation of the particle shape by controlling the injection flow rate and the balance of the concentrated raw material.
When high-concentration raw materials are sprayed at ultra-high pressure, they are forcibly drawn in and dispersed by oblique collision due to the negative pressure generated.
Application: Dispersion, pulverization
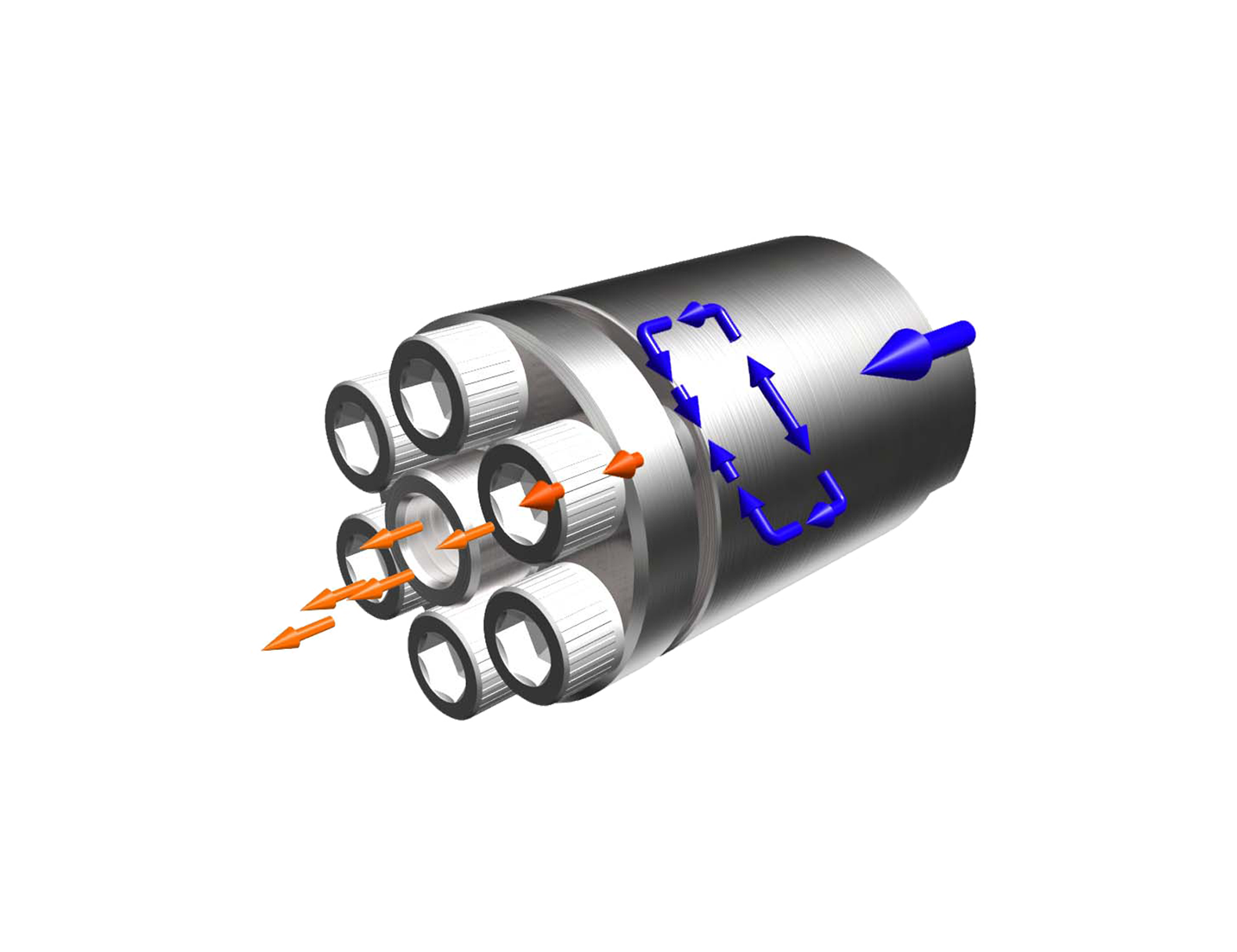
Slit Type Chamber (for emulsification)
Emulsification is performed when raw materials pass through the gaps (slits) between diamonds at ultra-high pressure.
Emulsification of cosmetics, foods, and pharmaceuticals is generated by a stronger shearing force than oblique collision.
Application: Emulsification
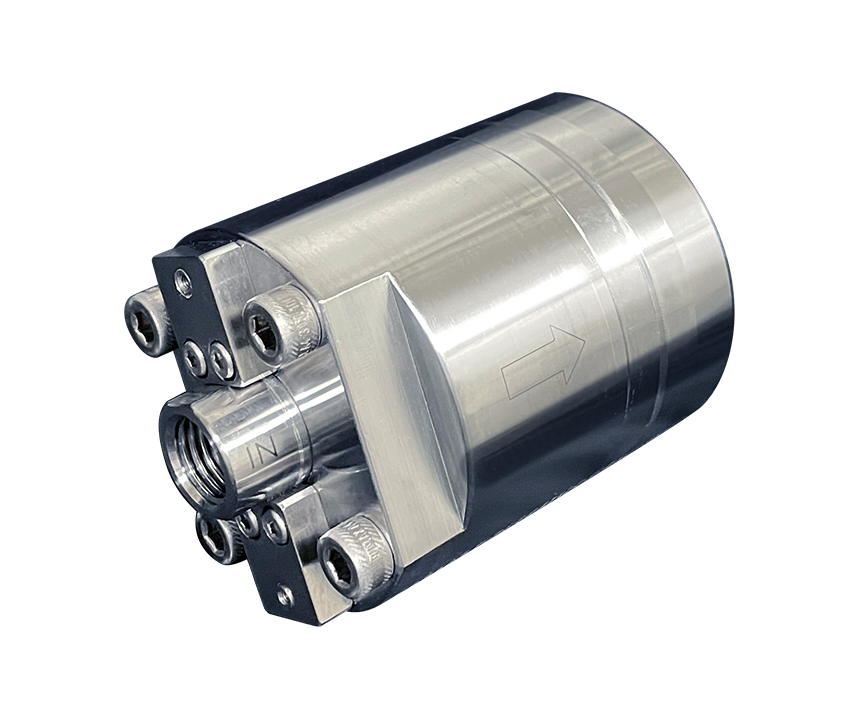
Ultra-Fine Slit Chamber
The newly introduced Ultra-fine Slit Chamber is recommended for grinding, dispersing, and emulsifying various ceramics, pigments, cosmetics, and comestibles.
This chamber has a narrower nozzle, delivering greater shear force than the current slit chamber. The updated design allows for faster and finer grinding, dispersion, and emulsification with minimal contamination.
Testing indicates that wet milling with the Ultra-fine Slit Chamber can pulverize silicon, graphene, CNT, and other materials finer than with conventional chambers. Current trials have achieved pulverization of some raw materials to 1/5 the size of the current slit chamber.
Compared to the Slit Chamber, the new Ultra-fine Slit Chamber achieved emulsification rates 400% faster, 26% smaller particles, and improved liquid transparency.
Particles and droplets can be reduced to sizes unachievable with conventional slit chambers, improving final product performance and fueling innovation.
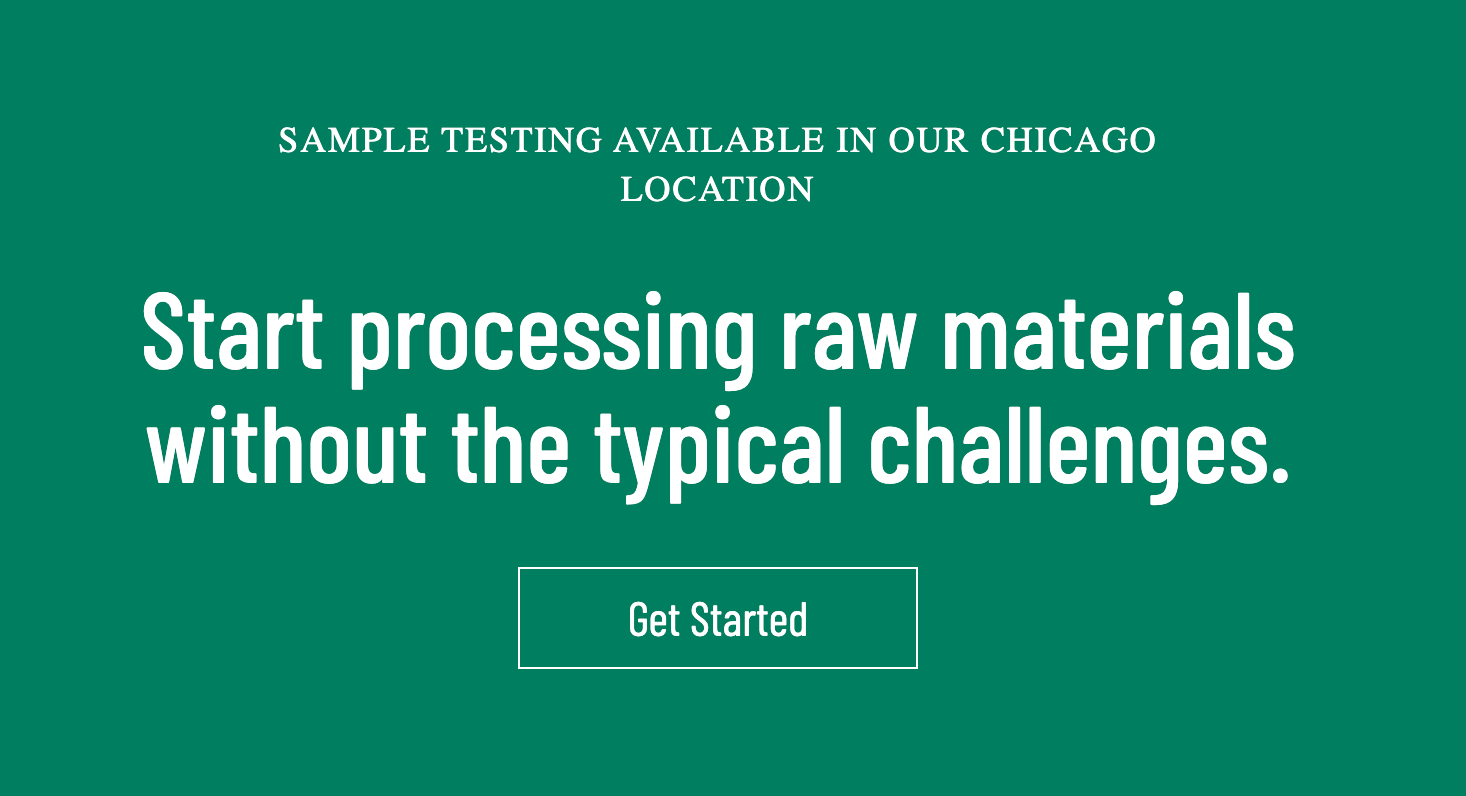